FILAMENT DRYING KITS
EVERYTHING YOU NEED
TO DRY YOUR FILAMENTS
Why does moisture matter for 3D Printing?
Overhang Quality
Surface Finish & Texture
The Drying Process
Our Methodology
Chamber + Pump kit Includes:
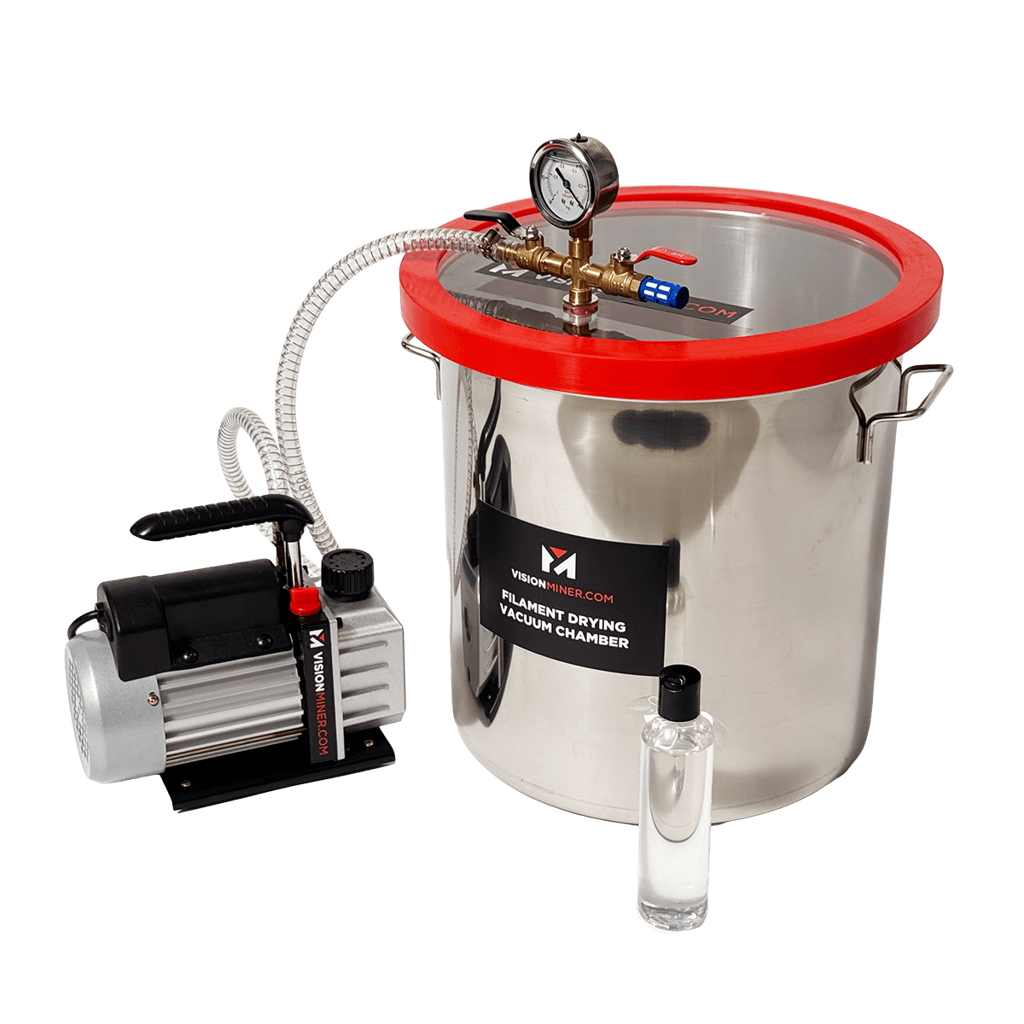
Material | Drying temp* | Drying time** | Max moisture content |
---|---|---|---|
PLA | 65-90°C | 4-12 hrs | 250 ppm |
ABS | 80-90°C | 2-4 hrs | 200 ppm |
PCTG | 65-70°C | 4-8 hrs | 600 ppm |
TPU A | 80-90°C | 2-3 hrs | 200 ppm |
TPU D | 90-120°C | 2-3 hrs | 200 ppm |
HTN | 110-110°C | 6-8 hrs | 400 ppm |
PA 12 | 80°C | 4-8 hrs | 1000 ppm |
PACF | 100-120°C | 4-8 hrs | 500 ppm |
PC | 120°C | 3-5 hrs | 200 ppm |
Essentium 9085 | 110-120°C | 4-6 hrs | 200 ppm |
PEEK | 120°C | 3-6 hrs | 200 ppm |
PEKK | 120°C | 3-8 hrs | 200 ppm |
PPS | 120°C | 2-4 hrs | 100 ppm |
PESU | 120°C | 3-4 hrs | 200 ppm |
PETCF | 90°C | 6-8 hrs | NA |
PPCF | 70°C | 2-4 hrs | 200 ppm |
* These temperatures are intended for a dehumidified hot air dryer, using air with a dew point below -40°C.
** The table shows estimated drying times based on common industry practices for different materials. If a spool has only absorbed a small amount of moisture, it can be dried more quickly, while more moisture requires longer drying times and higher temperatures. Materials like polyamides, polysulfones, TPU, PEI, and PVA are very sensitive to moisture and may need even longer drying times if they reach their maximum moisture capacity. To avoid issues, it's best to keep these materials dry and prevent them from absorbing too much moisture. When over-dried for long periods of time (generally days, weeks, or months) polymers can become brittle, so be careful not to over-dry.
My Wishlist
Wishlist is empty.